Production process
Manufacturing of wax models
The prepared wax mixture is injected under pressure into duralumin molds.
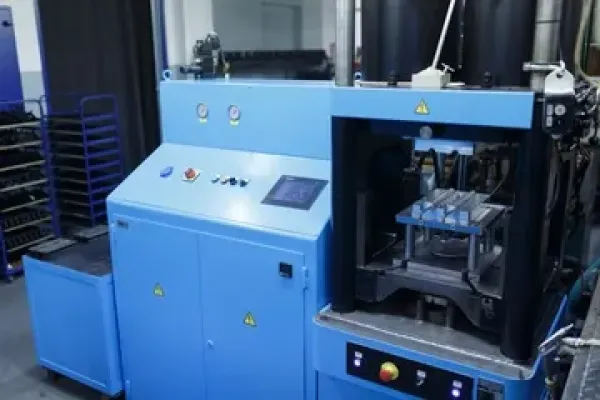
Assembling wax models for the tree
The wax models are assembled and soldered onto the gate system, creating what is known as a tree.
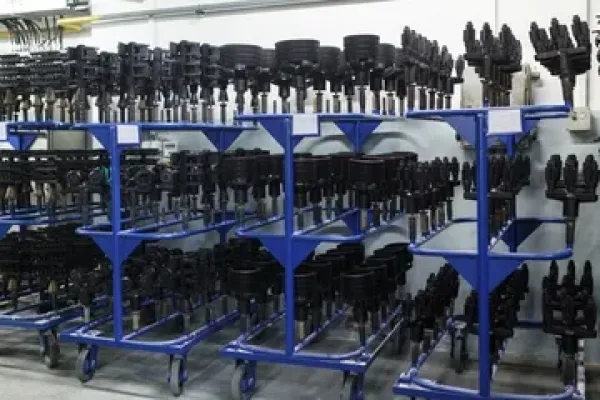
Soaking wax models in ceramic mixture and sand
The trees are dipped in a ceramic mixture based on SiO₂, coated with silica sands, and dried in air-conditioned spaces
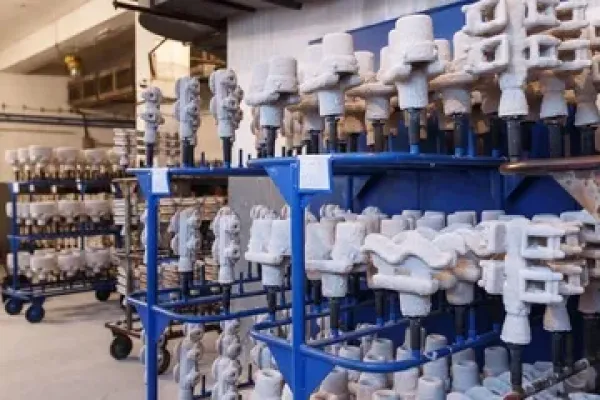
Wax melting in an autoclave
The wax is extracted from the shells in an autoclave using steam.
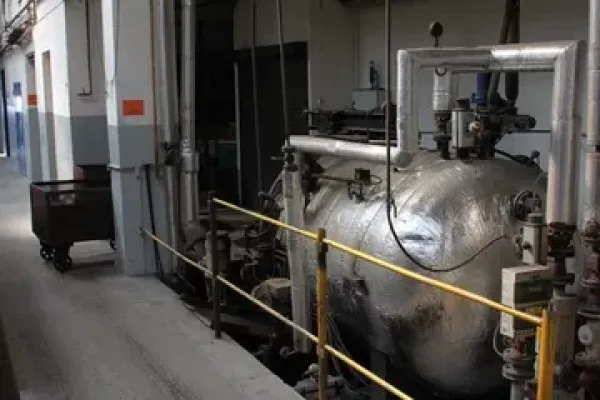
Casting
The metal melting takes place in medium-frequency open furnaces with a thyristor converter of 200 kW power and a capacity of 2 x 100 kg.
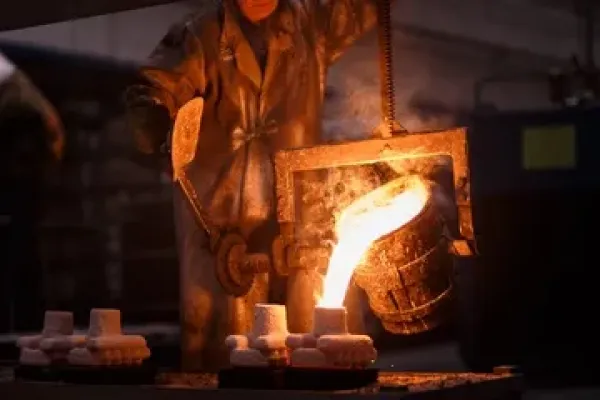
Removal of ceramics
After cooling, the castings are removed from the ceramic shell in a vibrating machine.
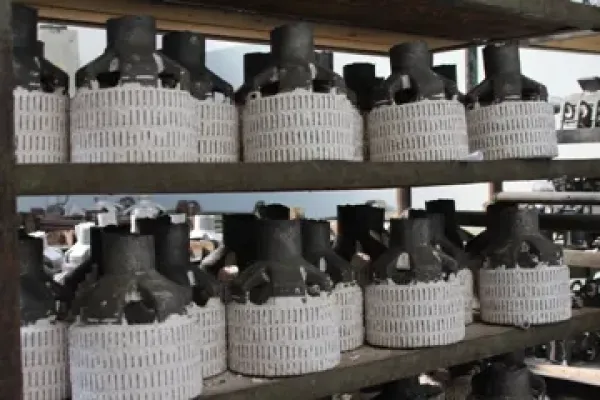
Finishing operations
Finishing operations are carried out on the castings to achieve the final finish:
- Pre-blasting in a chamber blaster
- Separation of castings on cutting machines
- Heat treatment
- Final blasting of castings with abrasive depending on the type of steel
- Machining, grinding, polishing, surface treatment
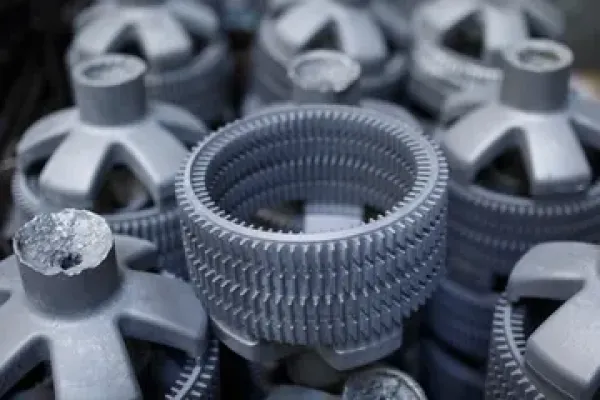
Machining
The machining of castings takes place on CNC and conventional machining machines to achieve the highest possible precision.
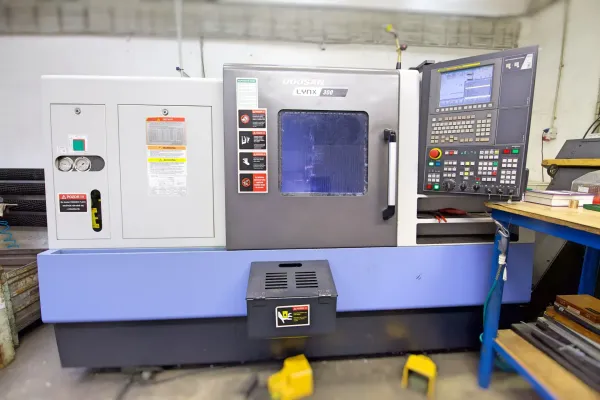
Visual and dimensional inspection
Each casting undergoes 100% visual inspection. For the first series, we perform dimensional checks of the wax models and castings (with the possibility of 3D measurement).
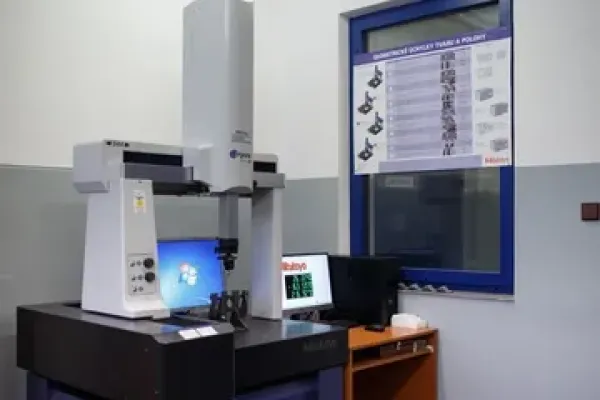
Packing and shipping
The finished castings are packed according to the specifications and requirements of individual customers and delivered on time.
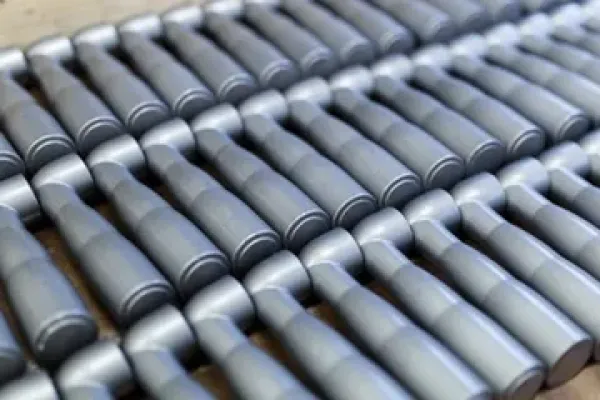