Castings
Prototypes
The printer for the Rapid Prototyping process
This innovative technology uses a method of applying liquid material to a printing plate, enabling the creation of wax models with exceptional design freedom. Models made of 100% wax are completed within a few hours, making it ideal for producing small series, prototypes, and unique parts.
Support software
We are now assisted with the design of the gating system by the simulation software Magmasoft. This software not only simulates the casting and solidification process, but also predicts potential internal defects or heterogeneous inclusions in the structure of the future casting. In addition, it optimizes the entire casting process according to predefined criteria, even at the early stage of technological preparation for production, directly within CAD data on the PC.
Technology
The advantage of precision casting technology is the ability to produce geometrically complex parts that closely resemble the optimal shape, while also utilizing materials that are difficult or completely impossible to machine.
Water-soluble, removable cores - this technology is used to create complex internal cavities and shapes in the casting that cannot be achieved with a standard metal mold for wax models.
This technology, however, requires the creation of a model device for the injection of soluble cores, with the wax REMET being used for the production of these cores
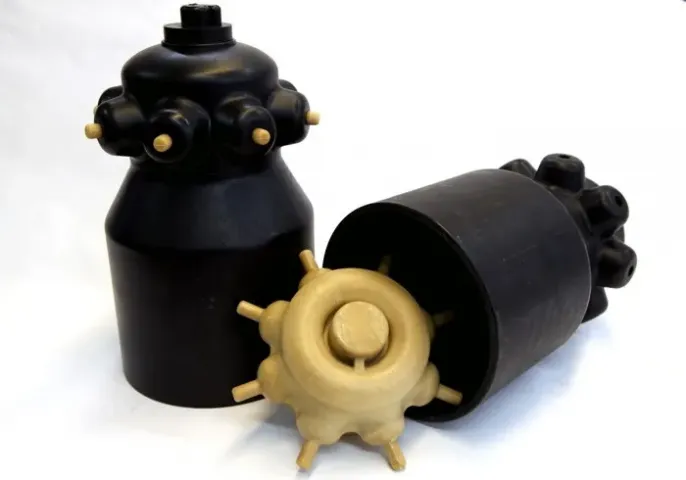
Thermal processing
In collaboration, we ensure the basic heat treatment of castings.
- normalizing annealing
- soft annealing
- Annealing for dissolution according to customer requirements
- hardening
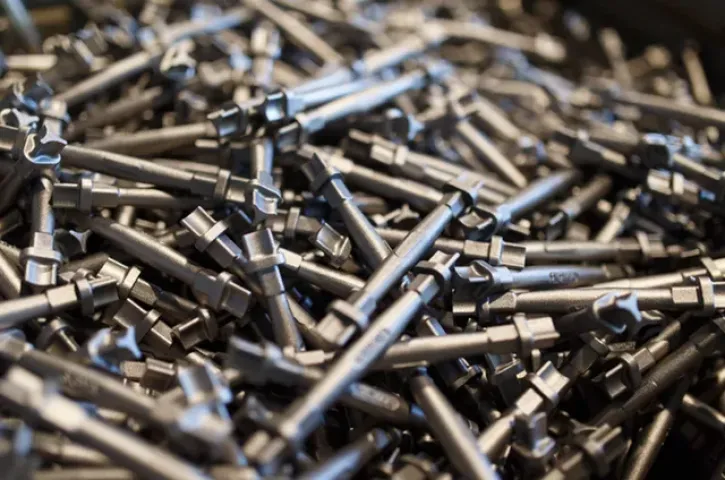
Parameters of Castings
Minimum weight : | 0.001 kg |
Maximum weight: | 5 kg |
Maximum dimensions: | 250 mm |
The minimum wall thickness: | 2 mm |
Surface roughness: | Ra = 6,3 (N9 dle DIN) |
Dimensional tolerances: | VDG P690 D1 |
Delivery terms | 4 - 6 weeks after the mold is made |
The delivery times for castings: | By agreement (based on seriousness, on the capacity capabilities of the foundry, etc.) |
The foundry capacity: 200 tons of castings per year.
Forms and Models
We process drawing documentation for castings, master models, molds, and auxiliary equipment. We work in 3D AutoCAD and SolidWorks.
In collaboration, we ensure the production of complex metal master models and molds made of steel or duralumin using the latest technologies.
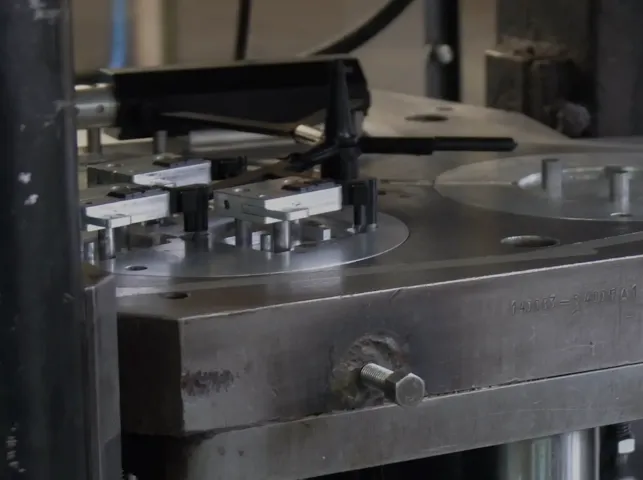
Materials
Our foundry focuses on the production of castings made from austenitic steels. Based on requirements, we can supply castings made from various steels according to ČSN and DIN standards, suitable for melting in open furnaces.
The following types of steel are used for casting production:
- carbon
- low and medium alloyed
- corrosion-resistant austenitic and martensitic
- instrumental
- heat resistant
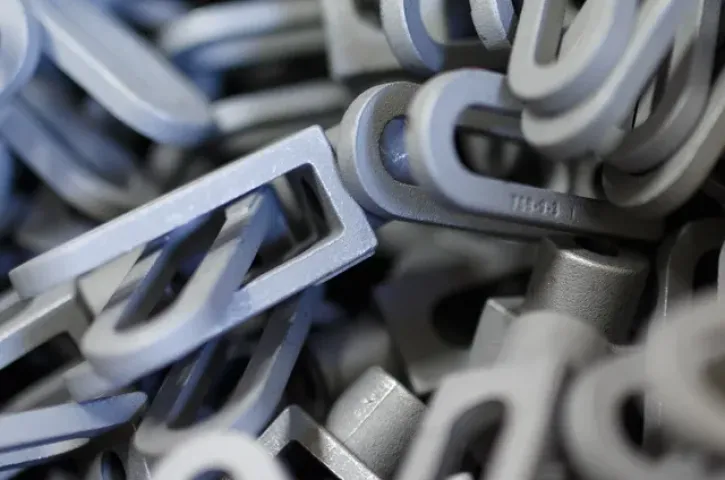
Finishing process
CNC machining
- Turning
- Drilling
- Grinding
Surface finishes
- Zinc
- Nickel plating
- Dyeing
- Polishing
Machining capacities
Machine name | Technology | Starts (mm) |
Fanuc Robodrill D21LiB5 | Multi-axis CNC milling | 700x400x330 |
Haas Super Minimill 2 | 3-axis CNC milling. | 500x400x300 |
Doosan Lynx 300 | CNC turning | Rotational diameter is 450, length 765. |
Doosan Lynx 2100 LY | CNC turning | Rotational diameter 300, length 300 |
Goodway GLS 200 | CNC turning | Rotational diameter is 400, length 500. |